Digital Design Month: Is This the Strategy We Need for Rebuilding American Manufacturing?
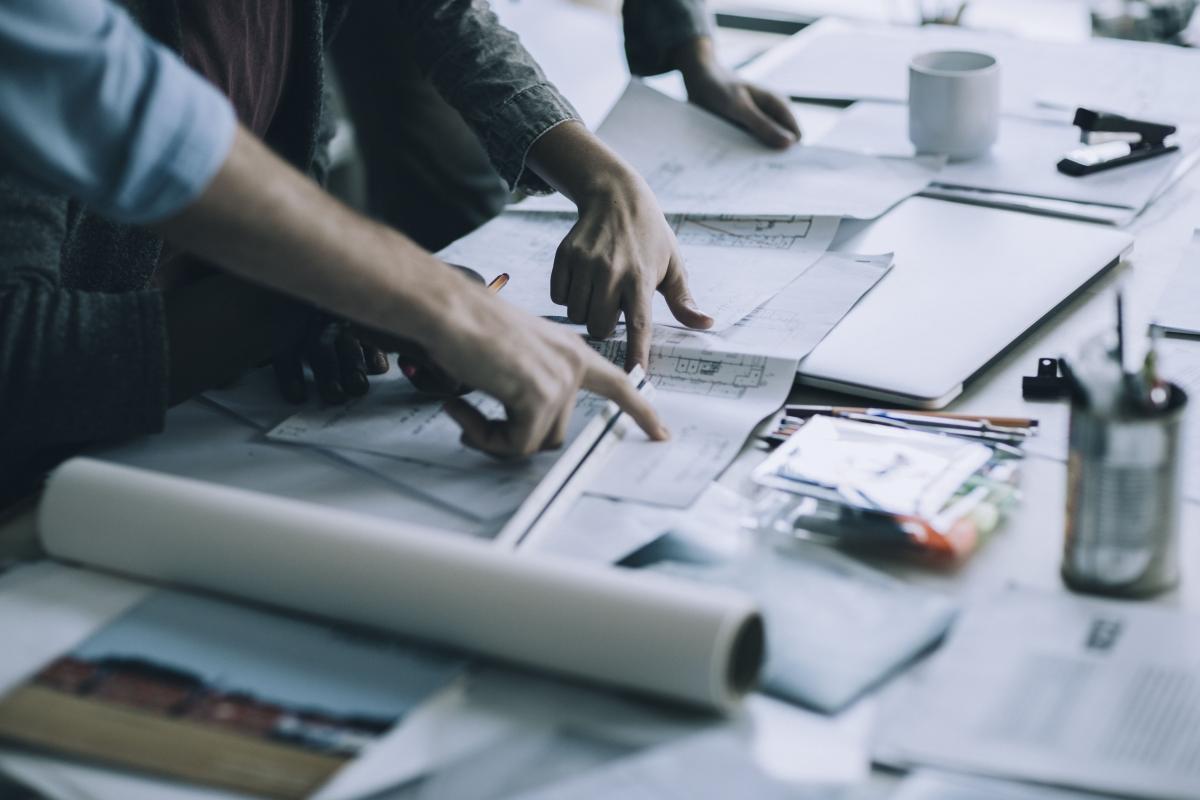
Bolstering the U.S. manufacturing sector is a message that has played into election campaign promises and White House administration policy for decades. The reality is a different story. As The Century Foundation, a nonpartisan think tanks, points out in its article – A Strategy for Rebuilding the Manufacturing Sector in the United States – investments in the manufacturing and design sector are being slashed particularly in areas ranging from scientific and engineering research to workforce education and skills.
The Century Foundation presents a powerful case for why rebuilding the manufacturing sector matters for several reasons. For example, studies show that products can be produced profitably in the U.S. by a well-paid workforce. Plus, a healthy manufacturing sector is critical to urban and rural communities.
There’s also a proven connection between advanced manufacturing processes and the research and development (R&D) efforts that feed into these processes. The argument being that if the U.S. lacks the manufacturing capability for certain products, it will also lose its R&D capacity and pioneering influence.
Finally, manufacturing jobs pay better than other jobs for those who lack a college degree and are critical to the economies of the Midwest and Southeast.
The Challenges of 21st Manufacturing
Key to bolstering this critical sector is understanding how manufacturing has evolved. Today’s industries are highly dependent on innovative science and technology, much of it developed in government-funded labs. From robotics to automation, industrial internet of things (IIoT) to new composite materials, how America manufactures is changing. Yet. finding the right manufacturing partners and a skilled labor force to move forward with manufacturing innovation is hard.
Foreign governments have responded to these challenges by creating programs that connect firms to cutting-edge technological resources and assist them as they scale up to mass production and help them develop go to market roadmaps. One such partnership in the U.S is the Manufacturing Extension Partnership (MEP).
According to The Century Foundation, “These partnerships can build a critical mass of technical experts that can assist manufacturers in product development, supply chain integration, and innovation…(for) every dollar invested in MEP generates an estimated $32 in in economic growth, which translated into $3.6 billion in new sales for the small- and medium-sized enterprises.”
Under President Obama, the U.S. created a manufacturing extension known as Manufacturing USA which invests in sub-sectors that show the most promise for maintaining American manufacturing leadership. The initiative is designed to improve manufacturing competitiveness and increase production of goods; advance the leadership of the U.S. in advanced manufacturing research, innovation, and technology; facilitate the transition of innovative technologies into scalable, cost-effective manufacturing capabilities; accelerate the development of an advanced workforce, and more.
There are currently fourteen Manufacturing USA institutes, each focusing on an advanced manufacturing technology, such as 3D printing, advanced composite materials, etc. Most institutes have only been in existence for a few years but have been eagerly welcomed by industry participants and the first eight institutes alone have 753 partners, mostly business firms. Successful projects to date include a collaboration between a West Coast technology company and a Midwest printing company to tap into the latter’s experience printing on flexible products. Another collaboration saw the Institute for Advanced Composite Manufacturing Innovation work with Oak Ridge National Laboratory on the use of 3D printing and new composite materials to produce an electric-powered replica of a Shelby Cobra car – the design and manufacturing took just six weeks, a testimony to the value of these new prototyping technologies.
3D printing, also called additive manufacturing, is a way of printing 3D components from a digital model. Plastics and metal alloys are the most commonly used materials for 3D printing, but it can work on nearly anything—from concrete to living tissue. In the public sector, the GSA’s 3D Printing Solutions is a spurring the use of such technology to assist agencies in:
• Rapid prototyping
• Obsolescent and legacy part manufacturing
• Reverse engineering
• Research and Development
• System integration
• Maintaining operational readiness
NASA, for example, is using 3D printing to test rocket parts to reduce future engine costs for its new heavy-lift rocket, the Space Launch System, among other projects.
Federal Policy Priorities for Rebuilding the U.S. Manufacturing Sector
Rebuilding America’s manufacturing capacity is a priority for all of us. But understanding how 21st century manufacturing differs from that of the 20th century is key, explains The Century Foundation. Tax breaks and other inducements are no longer effective. Instead, federal government should consider the following four policy priorities as outlined in the article:
1. Changes in government tax and spending policy to shift away from the winner-take-all model of economic growth.
2. Significant increases in federal research and development expenditures, including another $3 billion per year for advanced manufacturing and manufacturing extension.
3. Increased public investment in infrastructure that is coordinated with manufacturing initiatives to build domestic manufacturing capacity.
4. New financing mechanisms that provide support for small- and medium-sized manufacturing firms.
Progress can’t be achieved by the federal government alone. Public/private initiatives in state and local government must also play a role. Take a look at the case made by The Century Foundation. It’s a compelling insight into how manufacturing has evolved and what we as a nation can do to keep pace and nurture a stronger economy for all.
Related
3D printing – increasing readiness by manufacturing in the field